Case Studies
Camper Awnings
The Challenge
One of the largest manufacturers in the world of RV campers, based in the U.S, commissioned the development and construction of a hot air welding machine that would produce camper awnings in high volumes. The seams were required to be both aesthetically pleasing and extremely durable to withstand the tension on the awning’s surface, including the fact that the produced awnings would be frequently opened-and-shut.
The Solution
Using the based concept of our SM-450-SA-series multi-sealer, we designed a multiple welding head machine with hot air technology. The machine fed the PVC-coated fabric from a heavy duty motorized unwinding station with automatic edge correction and digital fabric tension control.
To optimize the customer’s manufacturing process and reduce downtimes, we built an unwinding system with the ability to accommodate two jumbo rolls. This way, when the first roll finishes, the operator can immediately insert the second roll and seamlessly continue the welding cycles. While the second roll is being processed, the first roll could then be substituted.
High speed manufacturing
We installed two high-power welding heads on the left and right side of the tool bridge to fold the fabric into a pocket and insert the core that is used to attach the fabric to the awning structure. As the machine works at exceptionally high speeds (up to 15 m/m), we integrated an accumulator before the cross-cutting station so that the machine does not have to slow down or come to a full stop, instead continuing the welding process during the cut.
In addition, we designed the cutting tool so that it could cut in both directions (left to right and right to left) in order to avoid from having to make a back-and-forth motion that would have increased the cycle time.
This machine was successfully installed in the customer’s main factory in the U.S.
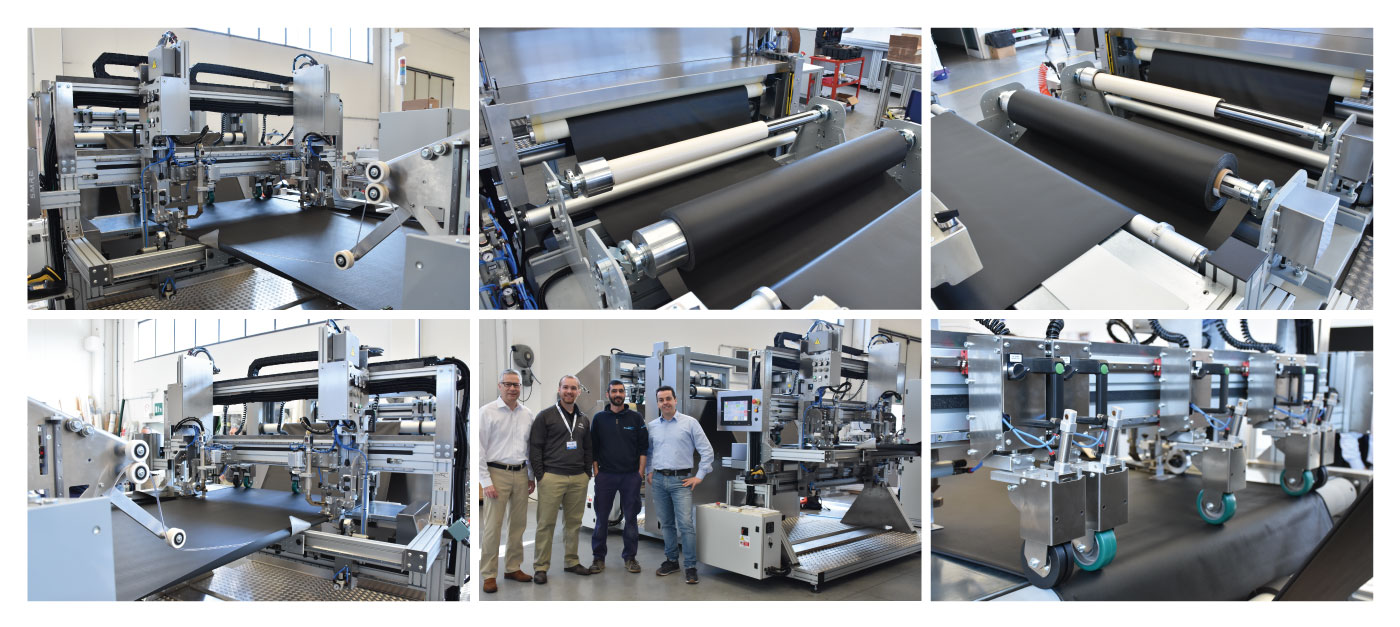